6063 VS 6005: A Detailed Comparison of Aluminium Alloy
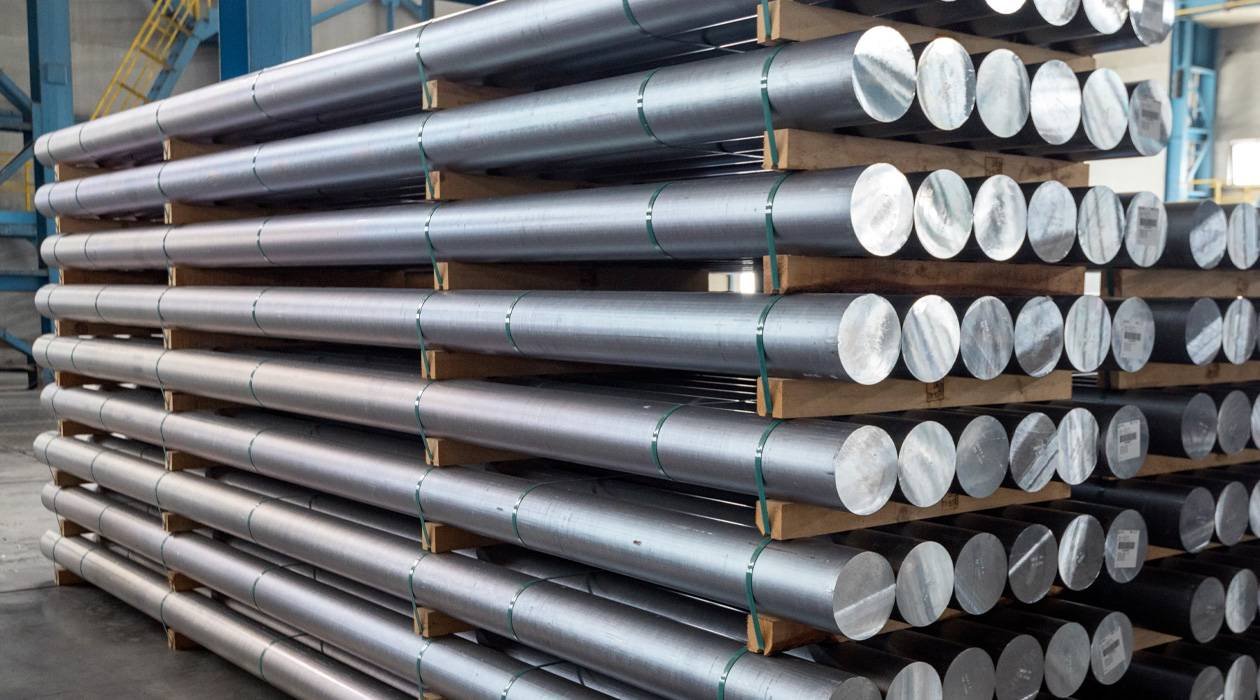
6063 and 6005 aluminum alloys both belong to the 6000 series aluminum-magnesium-silicon alloys. They share similar corrosion resistance and workability, but they differ significantly in composition, performance, and application. By comparing the two, you can better understand their respective advantages and usage areas.
Similarities:
- Main Alloying Elements:
6063 and 6005 share magnesium (Mg) and silicon (Si) as their primary alloying elements. Both form Mg₂Si (magnesium silicide) in the aluminum matrix, which enhances the alloy’s strength and hardness through heat treatment. - Good Corrosion Resistance:
Since both are aluminum-magnesium-silicon alloys, they have natural oxidation resistance. They form an aluminum oxide film when exposed to the atmosphere, providing excellent corrosion resistance. This makes them suitable for external structures, transportation, and marine applications. - Workability:
Both alloys have excellent workability and can be processed through various manufacturing methods such as extrusion, welding, drilling, and bending. Extrusion is especially important as 6063 and 6005 are widely used to create complex cross-sectional aluminum profiles. - Heat Treatability:
Both can be heat-treated to adjust their mechanical properties. Common heat treatment tempers include T5 (partially heat-treated, air-cooled, and artificially aged) and T6 (fully heat-treated, solution heat-treated, and artificially aged), which improve strength, hardness, and wear resistance. - Environmental Sustainability:
One important characteristic of aluminum alloys is their recyclability. Both 6063 and 6005 are low-cost to recycle, and their mechanical properties remain mostly unaffected by recycling. This makes them highly sustainable, aligning with the demands for environmental and circular economy considerations in modern manufacturing.
Differences:
- Chemical Composition:
- 6063 contains about 0.45-0.9% magnesium (Mg) and 0.2-0.6% silicon (Si), while 6005 has higher magnesium content (0.6-0.9%) and a relatively higher silicon content (0.6-0.9%). These differences result in 6005 having higher strength than 6063 but with slightly reduced formability and extrudability.
- Mechanical Properties:
- 6063:
It offers moderate strength and is ideal for applications requiring excellent surface quality rather than high strength. Its surface treatment performance is outstanding, providing a smooth finish for anodizing, electrophoretic coating, etc.- Tensile Strength (T6 temper): about 205 MPa
- Yield Strength (T6 temper): about 170 MPa
- Elongation (T6 temper): 12%
- 6005:
6005 has significantly higher strength than 6063 and is used for structural parts requiring greater load-bearing capacity.- Tensile Strength (T6 temper): about 295 MPa
- Yield Strength (T6 temper): about 255 MPa
- Elongation (T6 temper): 8%
- 6063:
- Extrudability:
- 6063:
It has excellent extrudability, making it ideal for complex cross-sectional aluminum profiles. Therefore, it is widely used in building profiles such as window frames, door frames, and curtain walls. - 6005:
While 6005 also has good extrudability, its higher strength makes it slightly less suited to complex cross-sectional profiles compared to 6063. It is more commonly used for structural profiles rather than decorative ones.
- 6063:
- Weldability:
- 6063: Excellent weldability, suitable for conventional welding techniques such as gas welding and arc welding. After welding, its surface is relatively easy to finish and repair.
- 6005: Slightly less weldable than 6063, with higher hardness after welding. Additional heat treatment may be required to improve the properties of the welded area.
- Applications:
- 6063:
Mainly used in applications requiring high surface finish and moderate strength. Common applications include construction profiles (door and window frames, curtain walls), decorative parts, furniture, solar panel frames, and heat sinks. Its good anodizing performance makes it ideal for visually appealing products. - 6005:
Due to its higher strength, 6005 is more suitable for structural applications such as load-bearing parts, components in rail transportation, ladders, stair railings, heavy-duty structures, and large industrial frames. Its hardness and strength allow it to withstand higher stresses.
- 6063:
- Hardness and Durability:
- 6005 has significantly higher hardness than 6063, making it better suited for environments requiring higher pressure or mechanical stress, such as mechanical components, bridges, and support structures in engineering.
Conclusion and Selection Recommendations:
- 6063: If your application focuses on aesthetics, surface treatment quality, complex cross-section design, and requires only moderate strength, 6063 is the better choice. It is ideal for windows, curtain walls, heat sinks, and decorative aluminum profiles, especially in cases where high surface finish is required.
- 6005: If your application demands higher strength and hardness, along with a need for materials that can bear load and provide structural stability, 6005 is the better choice. It is more suitable for engineering structures, rail transportation equipment, large mechanical frames, and similar applications.
Each alloy has its specific application scenarios. Depending on the requirements for strength, workability, and surface treatment, the appropriate material type can be selected.
We shanghai have different alloy for your different purpose! #shanghaislink
I loved as much as you’ll receive carried out right here.
The sketch is tasteful, your authored material stylish.
nonetheless, you commsnd get bought an impatience over that you wish be delivering the following.
unwell unquestionably come more formerly again as exactly the same nearly
very often inside case you shield this increase.